What is a Spring Washer?
A spring washer is a single, circular, fastening component possessing deflection properties that provide spring tension in bolted assemblies. They are able to withstand a wide range of pressures and are often a cost savings solution when space requirements and assembly weight are design factors.
What are Spring Washers Used For?
Spring washers are a popular fixture used in assemblies to reduce vibration, take up end play from wear or excessive tolerances, and keep mechanically fastened joints together.
What is the Difference Between Spring Washers, Wave Washers, and Lock Washers?
Spring washers encompass a group of washers that feature deflection properties. This includes wave washers and most lock washers such as toothed, split lock washers, and curved. The difference between wave washers and lock washers is that lock washers are used to provide pressure in bolted assemblies whereas wave washers typically are used for applying preload to moving assemblies.
What are the Different Types of Spring Washers?
The major spring washer groups include conical washers, curved washers, finger washers, waveform washers, and lock washers. We've split out the major groups of spring washers below:
Belleville Washers
Also known as conical or disc spring washers, they provide the greatest load‑bearing capacity for their size. They compensate for joint expansion and contraction, span holes, and maintain high tension in screw and nut assemblies. By combining them in varying sequence, each size gives numerous load carrying possibilities.
Key Benefits: Precise dimensional tolerance. Load deflection curve can be linear or non‑linear depending on height to thickness ratio. Can be stacked in different configurations to change deflection properties.
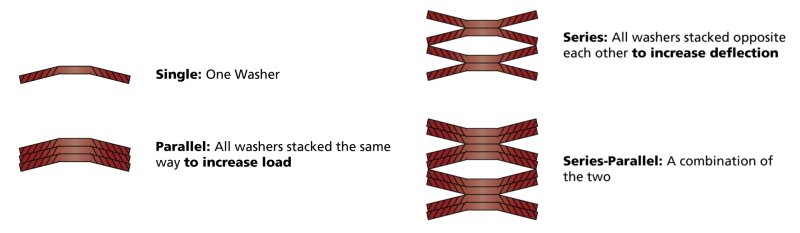
Curved Washers
Also known as single wave spring washers or cylindrically curved, they exert relatively light thrust loads and are often used to absorb axial end play or as lock washers for fasteners. The height of the form and material thickness are variables which can be adapted to a specific load/deflection function.
Key Benefits: Linear spring rate. Suitable for light loads in repetitive motion cycles.
Finger Washers
Counteract excess wear, vibration, noise, and end play. They promote efficiency and smooth operation, reducing skidding wear on rotating elements. They are also extremely useful in cases of unavoidable loose internal clearances due to special application conditions. Frequently used for preloading ball bearings and general applications.
Key Benefits: Combined qualities of curved and wave washers in one fastener.
Wave Washers
Also known as waveform washers, they provide greater load‑bearing capability because of their three‑point contact and sharper curves or waves. They are typically used in thrust‑loading applications for small deflections, particularly where radial space is limited. Applied loads are evenly distributed and there are not sharp edges to interfere or gall. The height and material thickness regulate the load function.
Key Benefits: Linear until washer is almost flat. Expands less on compression than curved washers. Often used for bearing preload and shock absorption.
Helical Spring Lock Washers
Also known as split lock washers, they are designed to apply spring pressure to mating threaded assemblies, creating frictional tension between threads. Slight trapezoidal cross section, coiled so that the free height is about twice the thickness of the washer section.
Key Benefits: A common, cost effective solution for decreasing risk of loosening caused by vibration. Used with wood, metal, plastic, and composite work pieces.
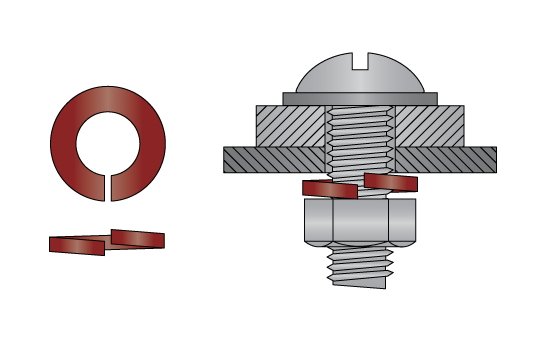